TC11鈦合金大型燃機(jī)轉(zhuǎn)子零件結(jié)構(gòu)采用電子束焊接方法實(shí)現(xiàn)整體制造 。 受接頭型式 、 鍛件冶金質(zhì)量 、 零件表面狀況及焊接工藝等諸多因素的影響 , 電子束焊接過(guò)程中可能會(huì)
形成工藝缺陷 。 這些工藝缺陷包括內(nèi)部氣孔 、 裂紋和局部凹陷 ( 低于焊后機(jī)械加工面尺寸 ) 等 , 焊縫裂紋和表面凹陷以及超岀焊接質(zhì)量檢驗(yàn)標(biāo)準(zhǔn)規(guī)定尺寸的內(nèi)部氣孔都必須修復(fù)補(bǔ)焊 。 補(bǔ)焊方法為手工鎢極氬弧焊 , 填充材料為 TA0 純鈦焊絲 。
對(duì)挖排后的缺陷采用氬弧焊補(bǔ)焊 , 因填充 TA0 純鈦焊絲導(dǎo)致缺陷區(qū)域重新熔融合金化,可能會(huì)形成該焊接區(qū)域的微觀組織差異 , 影響該區(qū)域的力學(xué)性能 , 另外 , 隨挖排和補(bǔ)焊區(qū)
域大小 ( 尺寸 ) 的不同 , 其影響程度也可能不相同 。 因此 , 有必要針對(duì)電子束焊縫不同類型 、 不同深度和尺寸的超標(biāo)缺陷開(kāi)展相應(yīng)的補(bǔ)焊工藝研究 , 評(píng)定補(bǔ)焊措施和補(bǔ)焊工藝對(duì)零件電子束焊接接頭質(zhì)量和力學(xué)性能的影響 。
1、試驗(yàn)材料與過(guò)程
試驗(yàn)使用的材料為TC11 鈦合金板材 , 其化學(xué)成分見(jiàn)表1 、 力學(xué)性能見(jiàn)表 2 。 試板規(guī)格為 400mm x 150mm x 15. 5mm( 帶鎖底 ) 及 400mm x 150mm x 8. 5mm 。 兩塊試板經(jīng)電子束焊接后 , 在焊縫上選擇 6 處位置 ( 編號(hào)依次為 : 1 、 2 、 3 、 A 、 B 、C ) 進(jìn)行機(jī)械挖排來(lái)模擬電子束焊接超差缺陷 , 然后進(jìn)行手工氬弧焊補(bǔ)焊工藝試驗(yàn) 。
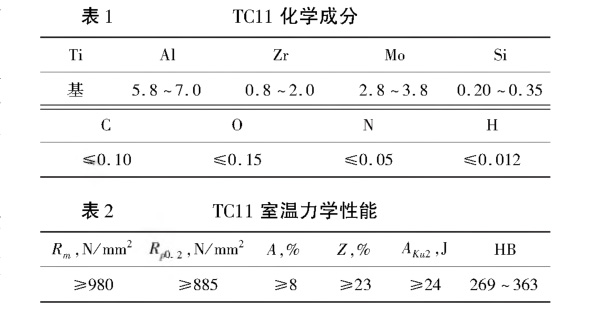
由于通過(guò)焊縫的 X 射線檢測(cè)光片只能確定缺陷尺寸 , 不能確定缺陷的深度位置 。 根據(jù)零件焊縫缺陷可能存在的深度和零件接頭處加工后的最終尺寸 , 對(duì)模擬缺陷的挖排深度
采取由淺至深原則 , 最終確定缺陷補(bǔ)焊試驗(yàn)缺陷的挖排深度分別為 2mm 、 5mm 和 8mm 。
采用手工機(jī)械磨削方式 , 對(duì)電子束焊接超標(biāo)缺陷進(jìn)行挖排,缺陷挖排后狀態(tài)如圖 1 所示 。
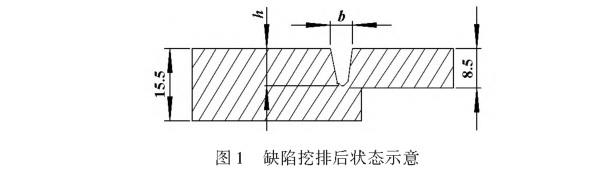
焊前對(duì)挖排區(qū)域表面嚴(yán)格清理 , 采用手工氬弧焊工藝進(jìn)行補(bǔ)焊 , 填充材料為 0 2.0mm 規(guī)格的 TA0 純鈦焊絲 , 氬弧焊焊機(jī)型號(hào)為 : PRESTPTIG 300 AC/DG 。 手工鎢極氬弧焊補(bǔ)焊工藝按照 HB/Z 120( 鈦及鈦合金鎢極氬弧焊接工藝 》 規(guī)定執(zhí)行 ,所采用的焊接工藝參數(shù)見(jiàn)表 3 。
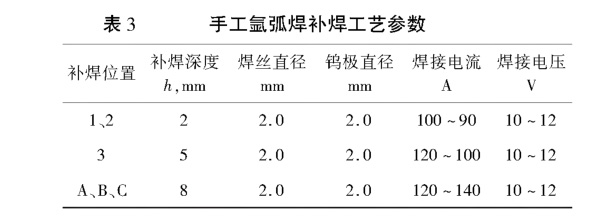
對(duì)氬弧焊補(bǔ)焊后的試板進(jìn)行 X 射線無(wú)損檢測(cè) , 焊縫質(zhì)量滿足 H255.105. 111 -89 《 電子束焊檢驗(yàn)和允許的缺陷 》 I級(jí)要求 。 補(bǔ)焊合格的焊接試板隨實(shí)際零件進(jìn)行熱處理 , 熱處理制度為 (530 ±10)t/(11 ~12)h,FC o在氬弧焊補(bǔ)焊過(guò)的 6 處位置取樣 , 并加工成厚度為 6mm的標(biāo)準(zhǔn)拉伸力學(xué)性能試樣 , 拉伸工作區(qū)寬度為 20mm 。 為保證所取力學(xué)性能試樣包含補(bǔ)焊區(qū)域 , 取樣時(shí)沿試板上層取 。加工完成的試樣再進(jìn)行 X 射線檢測(cè) 。
2、試驗(yàn)結(jié)果與分析
2.1 挖排缺陷深度為 2mm 的氬弧焊補(bǔ)焊
1 號(hào)和 2 號(hào)位置挖排深度為 2mm, 挖排區(qū)域尺寸分別為212mm x 6mm 和 14mm x 6mm 。圖 2 所示分別為 1 號(hào)和 2 號(hào)位置氬弧焊補(bǔ)焊前后的狀態(tài) 。
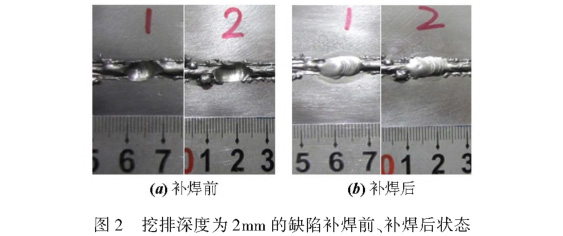
圖 3 所示分別為 1 號(hào)和 2 號(hào)位置補(bǔ)焊后加工去除焊縫余高和鎖底前后 X 射線底片的對(duì)比 。 由圖 3 可以看岀 , 在保留焊縫余高和鎖底狀態(tài)下, X 射線底片上并未發(fā)現(xiàn)有色差 。
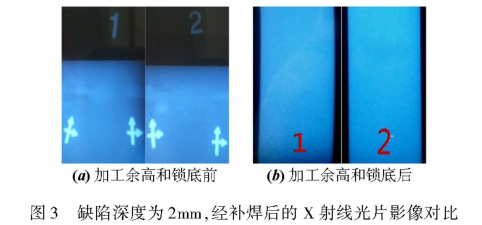
但經(jīng)機(jī)械加工去除焊縫余高及鎖底后 , X 射線光片影像顯示 , 補(bǔ)焊區(qū)域與原電子束焊縫相比 , 存在淺灰色影像的色差 。但由于該位置挖補(bǔ)深度較小 , 色差不太明顯 。
2.2 挖排缺陷深度為 5mm 的氬弧焊補(bǔ)焊
3 號(hào)位置挖排深度為 5mm, 挖排區(qū)域尺寸 12mm x 8mm,該位置氬弧焊補(bǔ)焊前后的狀態(tài)如圖 4 所示 。
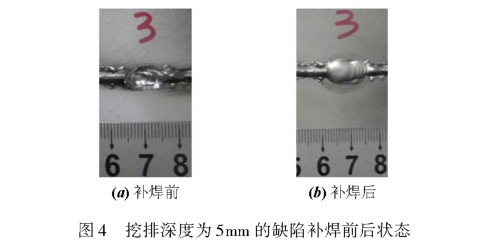
圖 5 所示為 3 號(hào)位置補(bǔ)焊后加工去除焊縫余高和鎖底前后 X 射線光片影像對(duì)比 。 可以看岀 , 在加工去除焊縫余高及鎖底后 , 補(bǔ)焊位置呈現(xiàn)淺灰色影像 , 與原電子束焊縫有較明顯的色差 。 其色差度超過(guò) 2mm 深度缺陷的補(bǔ)焊 2. 3 挖排缺陷深度為 8mm 的氬弧焊補(bǔ)焊挖排深度為 8mm 的位置分別為 A 、 B 、 C 3 處 , 其挖排區(qū)
域尺寸分別為 14mm x9mm 、 15mm x 7mm 和 13mm X 7mm 。
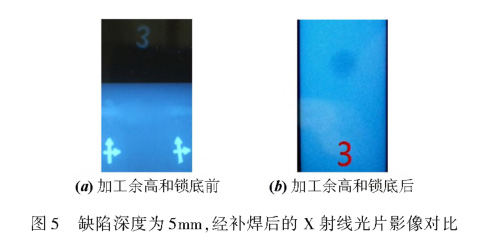
圖 6 所示分別為 3 處位置氬弧焊補(bǔ)焊前后的狀態(tài) 。
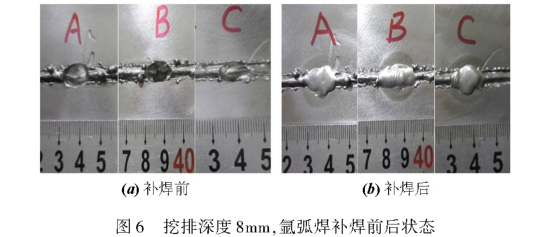
圖 7 所示分別為補(bǔ)焊深度為 8mm 時(shí)加工去除焊縫余高和鎖底前后 X 射線底片影像對(duì)比 。 從圖 7 可以看岀 , 在去除焊縫余高和鎖底前 , 由于余高和鎖底厚度對(duì)射線透射的干
擾 ,X 射線光片影像并未發(fā)現(xiàn)明顯色差 。 經(jīng)機(jī)械加工去除余高和鎖底后 ,X 射線光片影像顯示氬弧焊補(bǔ)焊區(qū)域同原電子束焊縫差異明顯 。 可以認(rèn)定 , 隨著挖補(bǔ)深度增加 , 填充的
TA0 純鈦焊絲在補(bǔ)焊熔池區(qū)域中的熔敷比也明顯增加 , 所形成的弧焊區(qū)域組織組成對(duì) X 射線透射率也增加 , 因此影像中的色差也明顯增加 。
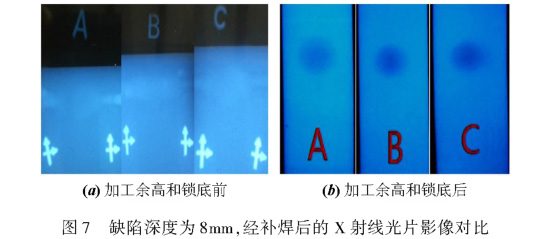
2.4 補(bǔ)焊深度及尺寸對(duì)接頭力學(xué)性能的影響
對(duì) 3 類缺陷經(jīng)補(bǔ)焊后的接頭截取標(biāo)準(zhǔn)的力學(xué)性能試樣 ,經(jīng)隨零件真空熱處理后進(jìn)行性能測(cè)試,測(cè)試結(jié)果見(jiàn)表 4 。
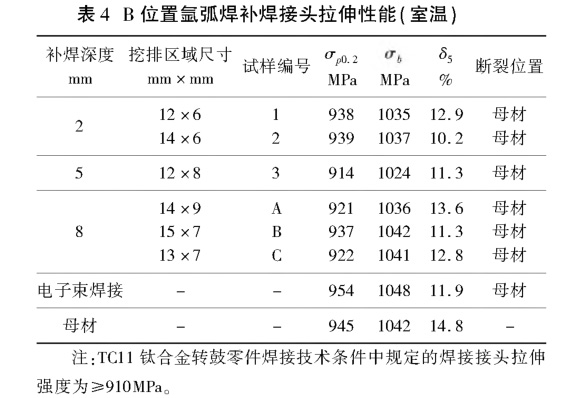
注 : TC11 鈦合金轉(zhuǎn)鼓零件焊接技術(shù)條件中規(guī)定的焊接接頭拉伸強(qiáng)度為 A910MPa 。
從表 2 可以看岀 ,3 種類型的缺陷經(jīng)補(bǔ)焊后的接頭力學(xué)性能較原電子束焊接接頭無(wú)明顯差異 , 性能試樣均斷裂在接頭母材部位 , 如圖 8 所示 。 可以認(rèn)為 , 其強(qiáng)度與零件 TC11 合
金母材相當(dāng) , 均能夠滿足技術(shù)條件中規(guī)定強(qiáng)度不低于 910MPa 的要求。
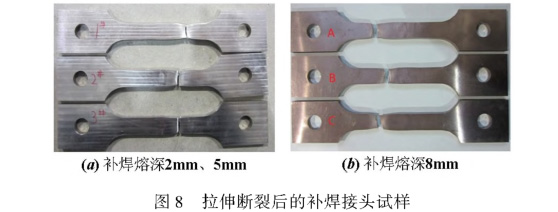
3、結(jié) 論
(1) 通過(guò)手工機(jī)械磨削方式挖排 , 并采用手工氬弧焊補(bǔ)焊工藝 , 能夠有效地排除零件電子束焊縫超標(biāo)缺陷 , 補(bǔ)焊工藝質(zhì)量能夠滿足技術(shù)標(biāo)準(zhǔn) H255. 105. 111 -89( 電子束焊檢
驗(yàn)和允許的缺陷 》 規(guī)定的 I 級(jí)焊縫要求 。
(2) 電子束焊縫缺陷的挖排 、 氬弧焊補(bǔ)焊工藝研究結(jié)果表明 ,3 種類型的缺陷經(jīng)補(bǔ)焊后的接頭力學(xué)性能較原電子束焊接接頭無(wú)明顯差異 , 性能試樣均斷裂在接頭母材部位 ; 其
強(qiáng)度與零件 TC11 合金母材相當(dāng) , 均能夠滿足技術(shù)條件中規(guī)定強(qiáng)度不低于 910 MPa 的要求 。
(3) 因填充 TA0 純鈦焊絲 , 補(bǔ)焊區(qū)域重新合金化 。 所獲得的組織組成和組織形態(tài)對(duì) X 射線的透射影響與原電子束焊縫不同 , 導(dǎo)致在 X 射線影像岀現(xiàn)不同程度的色差 。 隨著填
充量的增加 , 其透射程度增加 , X 光片的色差更加明顯 。
(4) 補(bǔ)焊結(jié)果表明 , 通過(guò)挖排和氬弧焊補(bǔ)焊工藝 , 并填充TA0 焊絲 , 能夠?qū)C11鈦合金轉(zhuǎn)子類零件電子束焊接生產(chǎn)過(guò)程的超差缺陷實(shí)施補(bǔ)焊修復(fù) , 同時(shí)也證明了本文的補(bǔ)焊工
藝合理 。
相關(guān)鏈接